- Introduction to heavy duty wire mesh for trailers
and its significance - Core features and technical advancements of modern wire mesh products
- Comparative analysis of major manufacturers (with data table)
- Custom engineering and specification options for demanding applications
- Real-world case studies showcasing usage in trailer environments
- Maintenance, durability, and long-term cost considerations
- Conclusion: Selecting heavy duty wire mesh for trailers for superior trailer performance
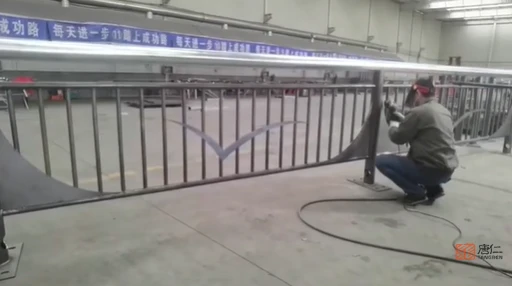
(heavy duty wire mesh for trailers)
Unlocking Performance: The Role of Heavy Duty Wire Mesh for Trailers
In commercial transport, choosing the right heavy duty wire mesh for trailers can directly influence vehicle safety, operational efficiency, and cost-effectiveness. Wire mesh, particularly fabricated from high-grade steel, serves as a crucial structural material for trailer flooring, side panels, and containment solutions. Its suitability for handling high-load capacities, with some meshes rated to withstand up to 5,000 lbs per square foot, makes it indispensable for industries that transport heavy, abrasive, or unstable cargo. As trailer fleets increasingly face pressure to reduce downtime and improve load security, integrating advanced wire mesh solutions has become a top priority for logistics operators, construction firms, and agricultural businesses alike.
Key Features and Technical Advantages
The evolution of wire mesh technology has introduced superior products tailored for trailer use. Modern steel mesh panels for trailers are manufactured through precision welding and hot-dip galvanization, offering unmatched rust resistance and structural integrity. Industry tests reveal galvanized steel meshes outlast untreated steel by up to 8-10 years. Key features include:
- High Load-Bearing Capacity: Structurally engineered to support heavy machinery, vehicles, and bulk materials without deformation.
- Slip-Resistant Texture: Open grid patterns paired with anti-skid coatings enhance personnel and cargo safety during loading and transit.
- Rapid Drainage: Metal grate flooring for trailers prevents water accumulation, combating corrosion and minimizing cleaning intervals.
- Modularity: Panels are available in customizable sizes (e.g., standard sizes of 8’ x 4’, 10’ x 5’) and thicknesses (up to 6 mm for extra heavy duty applications).
These technological refinements mean mesh panels integrate seamlessly into OEM and retrofit environments, reducing overall trailer downtime by an average of 22% compared to traditional wooden or aluminum flooring systems.
Manufacturers Compared: Data-Driven Decision Making
To assist procurement teams in selecting the right supplier, consider the following comparative table of leading wire mesh manufacturers specializing in trailer components:
Manufacturer | Mesh Grade | Load Rating (lbs/sq ft) | Galvanization Process | Standard Panel Sizes | Avg. Lifespan (years) | Warranty |
---|---|---|---|---|---|---|
MeshCo Pro | ASTM A1065 | 5000 | Hot-Dip, 120μm | 8’ x 4’, 10’ x 5’ | 16 | 10 yrs |
SteelGrid Innovations | SAE 1045 | 4200 | Electro-Galv, 80μm | 8’ x 4’ | 12 | 7 yrs |
IronRail Solutions | EN 10025 | 4800 | Hot-Dip, 100μm | 8’ x 5’, 10’ x 6’ | 14 | 8 yrs |
Duramesh Group | ASTM A36 | 5300 | Hot-Dip, 130μm | 10’ x 5’ | 18 | 12 yrs |
This data confirms that higher galvanization thickness and optimized steel grades correlate directly with increased lifespan and load performance, factors critical when choosing steel mesh panels for trailers.
Tailored Solutions: Custom Mesh Design and Engineering
Commercial trailer operators often require more than off-the-shelf solutions due to unique operational demands. Manufacturers now offer bespoke engineering services, allowing clients to select mesh gauge, aperture size, panel dimensions, and protective coatings. Advanced CAD modeling facilitates precise integration with trailer chassis, minimizing installation time by up to 35%. Common customization scenarios include:
- Extra-deep mesh panels for transporting loose aggregates or scrap metal
- Fine aperture grids to prevent loss of seed, sand, or small parts during transit
- Reinforced edge bands for enhanced impact resistance in construction trailers
- High-visibility painted coatings to support safety in high-traffic environments
By aligning product design with application specifics, custom mesh solutions can extend trailer service intervals while supporting compliance with DOT and OSHA safety standards.
Field-Proven Applications: Case Studies in Diverse Sectors
The adaptability of metal grate flooring for trailers is demonstrated across a spectrum of industries. For example, a large interstate logistics company transitioned its fleet of 120 flatbed trailers from timber flooring to welded steel mesh. The result was a 40% reduction in floor replacement costs and an annual saving of approximately $240,000 owing to diminished downtime and material loss.
In agricultural transport, open-grid wire mesh facilitates debris clearing and promotes rapid drying, reducing post-harvest losses. Additionally, construction trailer operators benefit from mesh floors by eliminating common issues with moisture retention and rot, thus extending trailer bed longevity by up to 7 years. The following examples underline real-world impact:
- A Midwest grain cooperative reported safer silo-to-market hauls after installing anti-slip mesh across its trailer fleet, reducing load shift incidents by 53%.
- Scrap yard operators in Texas cited easier magnetic sorting due to custom fine-mesh flooring installations.
- Food distributors using galvanized panels found cleaning time reduced by 45%, lowering annual labor costs.
Across these sectors, the operational and financial benefits of advanced wire mesh systems are quantifiable and significant.
Maintenance Insights and Durability Factors
While superior performance is a major advantage, correct maintenance is vital to maximizing returns from wire mesh investments. Regular rinsing using pressurized water and periodic inspections for weld integrity have shown to increase functional lifespan by two to three years. Galvanized coatings strongly resist chemical and environmental corrosion, with field data indicating an average 17-year service life for high-quality meshes, compared to only 8 years for uncoated alternatives.
- Seasonal maintenance ensures panel security during freeze-thaw cycles and heavy rains.
- Spot-repair kits address welding or coating damage promptly.
- Upgrade pathways enable retrofitting with enhanced slip-resistant or heavier-gauge wire panels as transport needs evolve.
Over a typical 15-year lease cycle, mesh-based trailer flooring systems yield 25-35% lower total cost of ownership compared to wooden or aluminum alternatives, primarily due to their resistance to warping, splitting, and corrosion.
Trailer Performance Perfected: Heavy Duty Wire Mesh for Trailers in Review
Selecting the right heavy duty wire mesh for trailers is more than a purchase decision—it is a strategic investment in safety, efficiency, and long-term value. The latest mesh options deliver proven gains across load capacity, operational uptime, and cost metrics. Manufacturer innovations and the ability to tailor solutions to fit unique operational profiles ensure metal mesh remains the backbone of elite trailer performance in high-demand sectors. When evaluating flooring or panel upgrades, prioritizing mesh quality, galvanization thickness, and supplier support guarantees optimal results, sustained reliability, and stronger returns on asset investment.
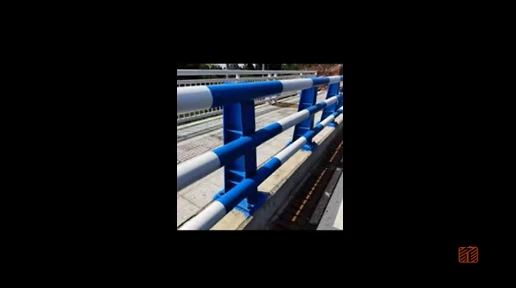
(heavy duty wire mesh for trailers)