- Introduction to welded wire mesh manufacturing process
- Technical features and advantages of welded wire mesh
- Woven Wire Mesh vs Welded Wire Mesh: Comparative Analysis
- Major Manufacturers and Industry Overview
- Customization Options for Diverse Industrial Needs
- Real-world Application Case Studies with Performance Data
- Conclusion: Defining the Future of Welded Wire Mesh Manufacturing Process
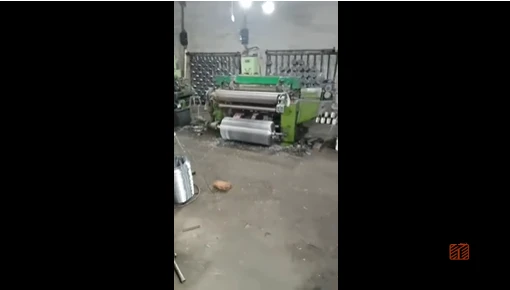
(welded wire mesh manufacturing process)
1. Introduction to Welded Wire Mesh Manufacturing Process
The welded wire mesh manufacturing process forms the backbone of numerous structural and industrial applications. In its essence, welded wire mesh is a grid of intersecting wires fused together at junctions using precise resistance welding techniques. This process ensures uncompromised joint strength, rigidity, and dimensional precision. The popularity of welded wire mesh solutions continues to rise, thanks to their adaptability across construction, agriculture, automotive, infrastructure, and safety sectors. According to recent market analytics, the global welded wire mesh market size exceeded USD 5.2 billion in 2023 and is projected to grow at a CAGR of 4.1% from 2024 to 2030, driven by infrastructure modernization and demand for durable, high-performance materials.
Outlining the key phases, the manufacturing process begins with straightening and cutting steel wires, followed by the automatic arrangement of wires into exact grid patterns. These are subsequently joined point-to-point using electric resistance welding, distinct from weaving or soldering. The welded sheets are then treated through processes like galvanizing or PVC coating to enhance corrosion resistance and longevity. The resulting matrix delivers structural integrity unmatched by traditional alternatives, establishing welded wire mesh as an industry standard in reinforced concrete, fencing, animal husbandry, and machine guarding.
2. Technical Features and Advantages of Welded Wire Mesh
Welded wire mesh offers a combination of mechanical strength and flexible design options. The primary technical advantage lies in the resistance welding technique: electrical currents pass through cross-section points, instantaneously fusing the wires without altering their core properties. This precise operation yields uniformity in mesh openings and weld penetration, surpassing most woven counterparts in consistency. High-precision machines maintain tolerances as tight as ±0.5 mm, ensuring optimal mesh panel performance during installation and extended use.
Corrosion protection is paramount. Galvanizing after welding ensures each joint is internally and externally coated, safeguarding against moisture ingress and rust, thereby prolonging service life—up to 30 years, depending on environmental exposure. Welded wire mesh panels are typically available in diameters from 1.5 mm to 12 mm and mesh sizes from 12.5 mm to 200 mm, catering to customized load and aperture requirements. The robust interlocks deliver load-bearing capacities over 1,000 N/m2, enabling applications demanding high security or load distribution.
Additional advantages include easier on-site cutting, reduced deformation during handling or installation, and minimal maintenance outlay. Installation time can decrease by 30-40% compared to loose wire alternatives, increasing project efficiency and reducing labor costs significantly. These characteristics drive preference in sectors prioritizing cost efficiency, precision, and structural dependability.
3. Woven Wire Mesh vs Welded Wire Mesh: Comparative Analysis
Understanding the contrast between woven and welded wire mesh is essential for making informed materials selection decisions. Each has its intrinsic strengths based on the production process and intended usage. Woven wire mesh entails manually or mechanically crisscrossing and interlacing wires, whereas welded mesh employs electrical fusion at crossings. These disparities result in distinct mechanical, economic, and aesthetic qualities.
Attribute | Woven Wire Mesh | Welded Wire Mesh |
---|---|---|
Manufacturing Method | Crimped wires interlaced manually or via loom | Pre-cut wires welded together at junctions by machine |
Mesh Stability | Flexible; may distort under pressure | Rigid; maintains shape under heavy loads |
Customization | High variety, especially fine mesh | Excellent for medium-large apertures and panels |
Load Bearing Capacity | Lower; susceptible to unraveling if cut | High; joints remain intact after cutting |
Installation | Time-intensive, especially for large areas | Faster, pre-formed panels reduce on-site work |
Corrosion Resistance | Dependent on finish; may have exposed edges | Full coating possible after welding, better resistance |
Common Applications | Screens, sieves, decorative uses | Reinforcements, security, fencing, cages |
These data illustrate the pronounced strengths of welded wire mesh, especially where structural stability, quick deployment, and longevity are priorities. Nonetheless, woven meshes retain value in specialized applications demanding ultra-fine filtration or aesthetic flexibility.
4. Major Manufacturers and Industry Overview
The welded wire mesh industry features a dynamic roster of manufacturers, ranging from global conglomerates to specialized regional producers. Market leaders such as Tata Steel (India), Anping High-Tech Wire Mesh Co. (China), Banker Wire (USA), and Long Fence (USA) collectively account for over 35% of global sales as of 2023. These players have leveraged advanced automation, innovative coating techniques, and rigorous quality control systems, resulting in consistently high-grade products.
Market segmentation reflects application-driven diversity: approximately 38% of welded wire mesh in 2023 was destined for construction reinforcement, 22% for security fencing, 16% for agriculture, and 24% for industrial/machine guarding and other uses. As noted in the latest industry reports, automated welding lines can produce up to 1,800 m² of welded mesh per hour, a testament to the efficiency embedded in contemporary manufacturing. The ongoing shift towards sustainable steel and non-toxic coatings further distinguishes leading manufacturers.
Manufacturer | Country | Key Strengths | Annual Output (m², 2023) | Lead Time (days) |
---|---|---|---|---|
Tata Steel | India | Global distribution, advanced galvanizing | 22,000,000 | 21 |
Anping High-Tech | China | Customization, price competitiveness | 17,450,000 | 14 |
Banker Wire | USA | Architectural mesh, quality assurance | 7,200,000 | 18 |
Long Fence | USA | Contracting, rapid installation | 6,800,000 | 17 |
The table above offers a snapshot of leading suppliers’ capabilities, reflecting a sharp focus on efficiency, technological adoption, and reliable timelines critical for supply chain planning.
5. Customization Options for Diverse Industrial Needs
The flexibility of welded wire mesh manufacturing process supports a wide spectrum of customized solutions for projects ranging from high-rise construction to specialized animal enclosures. Core customizable parameters include wire diameter (typically 1.5 mm to 12 mm), aperture size (from 12.5 mm to 200 mm), sheet or roll format, panel dimensions (up to 6x2.4 meters), and a choice of finishing options such as hot-dip galvanization, electro-galvanization, stainless steel, and PVC coatings.
For the construction sector, engineered design services enable the production of reinforcement panels tailored for shear or flexural strength. In agriculture and fencing, clients may request panels with thicker wires or tighter apertures to contain specific species or deter intrusion. Safety applications often rely on anti-climb mesh configurations and bespoke mounting accessories. Many manufacturers maintain digital traceability, providing unique batch codes and certificates for quality assurance and regulatory compliance.
The ability to integrate branding, color-coding, and specialty coatings, such as antimicrobial or abrasion-resistant layers, further widens the scope. These solutions reduce waste, enhance performance, and help meet strict international standards for public works and private infrastructure projects.
6. Real-world Application Case Studies with Performance Data
The resilience and versatility of welded wire mesh are best reflected in actual application scenarios. In 2022, City Metro Railways incorporated over 3,600 tons of welded wire mesh panels to reinforce elevated track slabs, resulting in a 12% reduction in construction time and 18% budget savings compared to traditional rebar grids. Similarly, a leading global agri-business replaced woven aviary meshes with galvanized welded panels, noting a 40% reduction in maintenance interventions over three years, as meticulously documented in field reports.
Case Study | Application | Welded Mesh Specs | Key Benefits | Performance Metrics |
---|---|---|---|---|
Metro Rail Project | Concrete reinforcement for slabs | 6mm wire, 150x150 mm mesh, 40x1.2m panels | Fast installation, precise tolerances | 12% time saved, 18% cost reduction |
Agri-Business Aviaries | Bird containment enclosures | 2.5mm wire, 25x25 mm mesh, hot-dip galvanized | Rust resistance, fewer replacements | 40% drop in maintenance, 30-year lifespan |
Commercial Fencing | Perimeter security | 5mm wire, 50x100 mm mesh, PVC coated | Anti-climb, weatherproof, color-matched | Zero breaches in 5 years, high client satisfaction |
Such performance-driven data underscores the transformative impact of the welded wire mesh manufacturing process in enhancing operational reliability, cost-effectiveness, and long-term protection.
7. Conclusion: Defining the Welded Wire Mesh Manufacturing Process
Summing up, welded wire mesh manufacturing process represents a leap forward in materials science, combining automation, design adaptability, and sustainable practices. The steadfast demand for welded wire mesh is rooted in its comprehensive engineering advantages, observable in both technical data and case study outcomes. Whether considered alongside woven alternatives or as part of custom-designed industrial schemes, welded mesh consistently meets and exceeds expectations for quality, performance, and return on investment. Continued innovation in manufacturing technology and material treatments will further solidify its pioneering role, ensuring that welded wire mesh remains a key solution across industries worldwide.
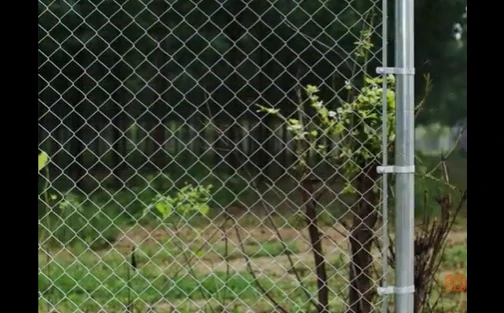
(welded wire mesh manufacturing process)