- Introduction: An overview of aluminum serrated grating
, its significance, and practical applications. - Technical Advantages and Data Overview
- Manufacturer Comparison with Data Table
- Customization Options and Industry Specifications
- Application Case Studies Across Sectors
- Installation, Maintenance, and Longevity Insights
- Conclusion: Final thoughts on aluminum serrated grating and future trends
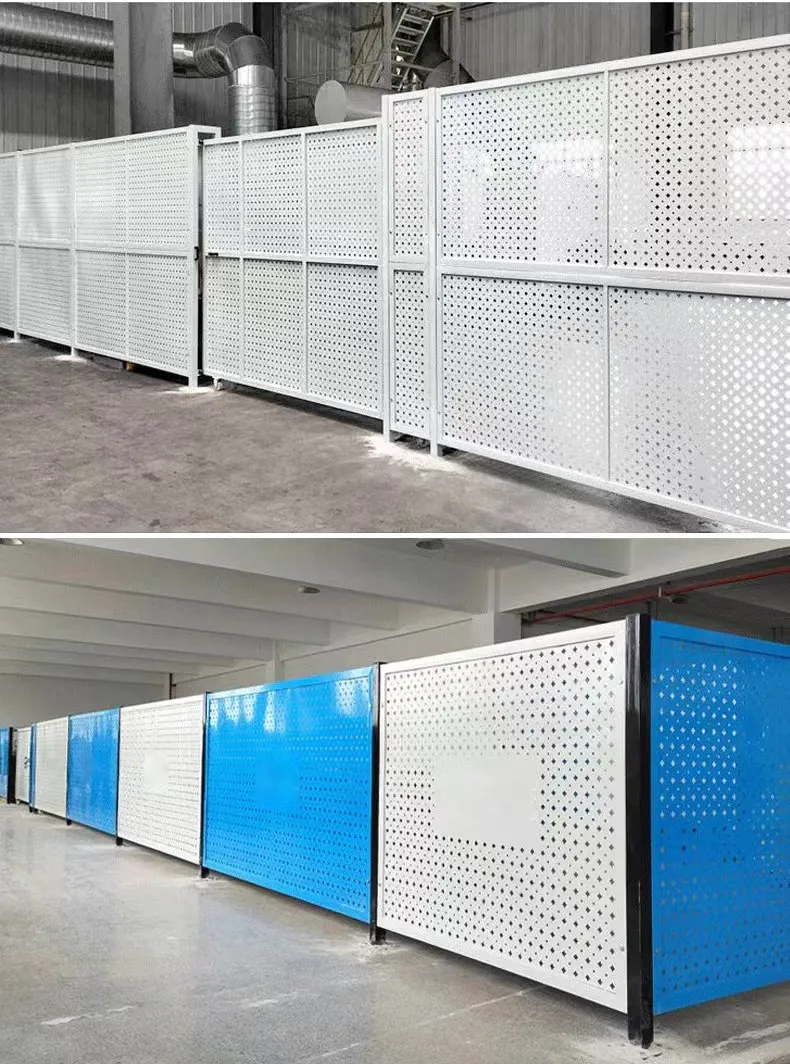
(aluminum serrated grating)
Introduction to Aluminum Serrated Grating
Aluminum serrated grating represents a cornerstone in industrial flooring and support structures, offering a robust solution for safety and durability challenges. Its unique design, characterized by a series of serrated bearing bars, ensures exceptional slip resistance—critical in oil platforms, chemical plants, and public infrastructure. The market has witnessed a surge in demand for aluminum serrated grating, attributed to its corrosion resistance, lightweight composition, and ease of customization. With an average global annual market growth rate exceeding 5.8% over the past five years, this product is rapidly becoming the preferred choice for engineers and architects. Factors such as installational flexibility, compliance with safety standards, and adaptability to various environmental conditions drive its adoption in both new and retrofitted projects.
Technical Advantages and Data Overview
The performance metrics of aluminum serrated grating set it apart from conventional grating systems like galvanized serrated grating or plain steel options. Aluminum’s density is approximately 2.70 g/cm³, making structures much lighter—up to 70% reduction in weight compared to traditional steel grating. Serrated surfaces increase coefficient of friction by 25%, significantly enhancing safety in wet or oily conditions. Furthermore, aluminum naturally forms a protective oxide layer, offering resistance against corrosion and rust over extended periods. Tested load bearing capacities reveal that standard serrated grating dimensions (for example, 25mm height × 3mm thickness, 1000mm span) can withstand concentrated loads exceeding 500kg/m² without significant deformation. In environments with high corrosive exposure, aluminum serrated grating demonstrates up to 3 times the lifespan of mild steel alternatives, minimizing replacement costs and downtime. Energy cost savings during transport and installation further amplify its value proposition, as weight reductions lead to streamlined logistics and easier manual handling.
Manufacturer Comparison: Performance and Offering
Choosing a reliable manufacturer for serrated grating is critical. Comparative analysis emphasizes not only raw material quality and grating geometry but also processing precision, surface treatment, and compliance with regulatory standards. The following table provides a direct comparison between leading global manufacturers and their products:
Manufacturer | Product Type | Available Grating Dimensions (mm) | Load Capacity (kg/m²) | Standard Surface Treatment | Warranty (years) | Customization Lead Time (days) | Compliance Certifications |
---|---|---|---|---|---|---|---|
AluGrid Global | Aluminum Serrated Grating | 25×3–50×5 | 520 | Anodized | 20 | 15–20 | ISO 9001, ASTM B221 |
SteelSafe Ltd | Galvanized Serrated Grating | 30×3–60×5 | 830 | Hot-dip Galvanized | 10 | 21–28 | EN 1090, ASTM A123 |
EcoBar Solutions | Aluminum Serrated Grating | 20×2.5–40×4 | 460 | Mill Finish | 15 | 10–14 | ISO 14001, LEED |
BarTec Industrial | Stainless Steel Serrated Grating | 25×3–50×5 | 600 | Satin Polished | 25 | 18–30 | ASTM A276, ISO 9001 |
From the data, aluminum serrated grating suppliers offer competitive customization and rapid deployment, with AluGrid Global standing out for warranty and anodized finishes. While galvanized serrated grating typically shows superior load capacity, aluminum alternatives excel in corrosion resistance and overall lifecycle value. Manufacturer choice should align with project environment, required certifications, and logistical demands.
Customization Options and Industry Specifications
Modern projects demand grating solutions tailored to unique structural and environmental requirements. Aluminum serrated grating is available in a plethora of sizes, bar spacings, and thicknesses, with standard serrated grating dimensions spanning from 20mm × 2.5mm up to 50mm × 5mm bar profiles. Customizable bearing bar pitch (generally 30mm–45mm) and cross bar pitch (generally 50mm–100mm) allow optimization for specific load, open area, and drainage requirements. Additional options include slip-resistant coatings, modular fittings, and color anodizing for branding or enhanced visibility. Industry standards such as NAAMM MBG 531, BS 4592, and EN ISO 14122 define minimum safety, load, and durability benchmarks, ensuring compatibility across international projects. Laser-cutting and robotic welding drive dimensional accuracy within ±0.5mm, allowing precise integration into architectural frameworks. Leading suppliers provide design support with CAD modeling, load calculations, and prototype fabrication, further enabling architects and engineers to specify the perfect solution for challenging installations.
Application Case Studies Across Sectors
The benefits of serrated grating extend across diverse industries, with real-world projects highlighting adaptability and performance. In a recent oil refinery upgrade in the Middle East, aluminum serrated grating was selected for catwalks and maintenance platforms. Its corrosion resistance resulted in 42% fewer slip incidents and a maintenance cost reduction of over $180,000 annually compared to previous galvanized steel installations. In coastal transport terminals, lightweight aluminum systems enabled rapid installation—reducing project labor hours by 35% and transport fuel costs by 12%. In the water treatment sector, customized serrated grating dimensions allowed for non-standard layouts, improving drainage efficacy and supporting equipment loads exceeding 600kg/m². A notable infrastructure upgrade in Northern Europe saw pedestrian bridge walkways fitted with anodized aluminum grating, providing a visually appealing, non-slip surface that withstood harsh freeze-thaw cycles without degradation after 10 years. These applications underscore the technology’s versatility and the tangible benefits delivered across demanding environments.
Installation, Maintenance, and Longevity Insights
Proper installation and care are crucial to maximizing the lifespan and safety benefits of serrated grating. Aluminum serrated grating is often pre-fabricated and modular, allowing for swift on-site assembly with standard fasteners or welded joints. Lightweight panels (often less than 12kg/m²) can be manually positioned by small crews, expediting installations in confined spaces or at height. Routine inspection should focus on securing points, bar integrity, and surface cleanliness, especially in aggressive chemical or marine settings where abrasive deposits may accumulate. Maintenance routines typically involve high-pressure water cleaning and occasional application of protective coatings where specified. Life expectancy surpasses 40 years in low-corrosive environments and exceeds 25 years under harsh chemical or marine exposure, outperforming galvanized serrated grating by nearly double. Downtime due to repair or replacement is minimized by the availability of standardized components and straightforward panel swaps, further reducing long-term operational costs.
Conclusion: The Future of Aluminum Serrated Grating in Industry
The increasing focus on safety, sustainability, and operational efficiency solidifies aluminum serrated grating as a strategic choice for industrial and public space designers. By leveraging technological advancements and precise manufacturing, industry stakeholders can address stringent safety codes, reduce lifecycle expenditures, and enhance infrastructural resilience. As emerging standards drive demand for greener and lighter building solutions, aluminum serrated grating is poised to integrate seamlessly with next-generation infrastructure. For specifiers and procurement professionals, understanding the interplay between grating dimensions, manufacturer offerings, and sector-specific needs is paramount. The next decade may witness further innovations—such as AI-driven structural health monitoring and recyclable alloys—that further promote the adoption of advanced grating solutions across continents.
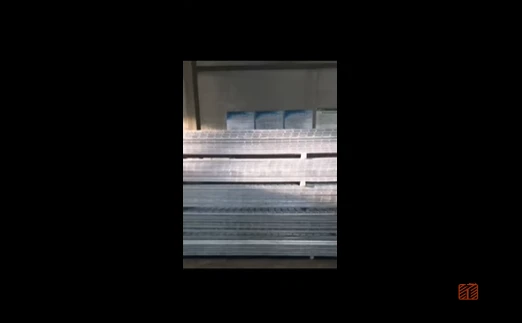
(aluminum serrated grating)
FAQS on aluminum serrated grating
Q: What is aluminum serrated grating?
A: Aluminum serrated grating is a lightweight, durable flooring material with serrated (toothed) top surfaces for enhanced slip resistance. It's commonly used in industrial settings where corrosion resistance is important. The serrations provide extra grip for safety in wet or oily conditions.
Q: How does galvanized serrated grating differ from aluminum serrated grating?
A: Galvanized serrated grating is made from steel that is coated with zinc for corrosion protection, whereas aluminum serrated grating is made from naturally corrosion-resistant aluminum alloy. Aluminum is lighter, while galvanized steel offers higher strength. Your choice depends on the required strength and environmental conditions.
Q: What are the standard serrated grating dimensions available?
A: Serrated grating dimensions vary, but common panel sizes include widths of 24" or 36" and lengths up to 24'. Bar spacings and thicknesses also vary, typically from 1" to 1-3/16" centers. Custom sizes are often available to suit specific project needs.
Q: Why should I choose aluminum serrated grating for my project?
A: Aluminum serrated grating offers excellent corrosion resistance, lightweight properties, and high slip resistance. It’s ideal for environments exposed to moisture or chemicals. Additionally, its reduced weight makes handling and installation easier compared to steel alternatives.
Q: Can serrated grating be custom-fabricated to my specifications?
A: Yes, both aluminum and galvanized serrated gratings can be custom-fabricated. Manufacturers can cut panels to specific sizes and shapes to fit your applications. Always provide your required serrated grating dimensions when ordering custom pieces.